Understanding Low Relaxation Testing in Prestressed Concrete Strands
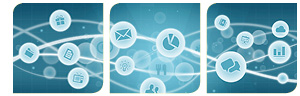
In the realm of modern construction, materials are expected to perform flawlessly under demanding conditions. One such critical property engineers and designers closely monitor is stress relaxation—especially in prestressed concrete structures. This is where Low Relaxation Testing becomes essential, particularly for seven-wire steel strands used in prestressed concrete applications.
What is Stress Relaxation?
Stress relaxation refers to the gradual reduction of stress in a material held under constant strain over time. For steel strands, this means that even if you maintain a fixed stretch, the internal stress will naturally decrease with time. This is a fundamental property of steel and significantly affects the durability and safety of prestressed concrete structures.
In simpler terms, if the tension in the steel decreases over time, the concrete it supports might not stay in compression—leading to cracks or even failure. Hence, ensuring low relaxation behavior in steel strands helps maintain structural integrity over decades.
Why is Low Relaxation Important?
Low relaxation strands offer a host of benefits, both economically and structurally. Here’s why they are widely preferred in high-performance infrastructure projects:
- Reduced relaxation losses: Lower than 2.5% stress loss over 1000 hours, compared to 5% in normal strands.
- Cost efficiency: Leads to 10–12% savings in overall construction costs.
- Structural performance: Enables longer spans (up to 25–30 meters), allowing for more innovative designs.
- Faster construction: Pre-stressed concrete with Low Relaxation Prestressed Concrete (LRPC) strands eliminates the need for post-straightening.
- Reliability and safety: Failures, if any, occur during manufacturing and not on-site.
- Enhanced fatigue resistance: This ensures lighter yet stronger structures.
From high-rise slabs and bridges to nuclear reactors and metro rail infrastructure, low relaxation strands have become an industry standard in performance-based design.
How is Low Relaxation Testing Conducted?
The test method involves evaluating the relaxation loss under a controlled temperature (typically 20°C) while maintaining 70% of the strand's specified breaking load.
- In Low Relaxation Prestressed Concrete Strands (LRPC), the acceptable relaxation loss is less than 2.5% after 1000 hours.
- In contrast, Normal Relaxation Prestressed Concrete Strands (NRPC) allow up to 5% relaxation loss over the same period.
This precise testing helps ensure that only high-quality steel strands make their way into critical infrastructure.
Real-World Applications
Low relaxation prestressed strands are widely used in infrastructure projects where long-term strength and reliability are critical. These include roads, bridges, flyovers, and metro systems, as well as high-rise building slabs. They are also essential in demanding environments like nuclear reactors, LNG tanks, dams, aqueducts, and jetties. Additionally, they support structural stability in railway sleepers, cement silos, rock anchoring, and soil stabilization projects.
Adhering to Standards
Low Relaxation Testing and material specifications comply with several international and national standards, ensuring uniformity and trust in performance:
- IS 14268
- ASTM A416
- BS 5896
- EN 10138
These standards guide manufacturers and construction professionals in delivering safe, efficient, and durable structures.
Final Thoughts
In conclusion, Low Relaxation Testing is not just a quality check—it’s a critical design input for civil engineers and architects. It ensures that prestressed concrete structures maintain their strength and shape over time, even under constant load.